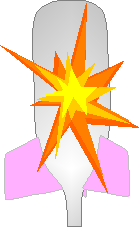
In the year 2000 I pioneered a new way to launch water rockets... using hydrogen combustion.
Internal combustion
Internal combustion is basically a controlled explosion (fuel and oxygen react) resulting in a hot pressurized gas in a confined space. In automobile engines the pressurized gas pushes a piston connected to a crankshaft. In my rockets’ case, the hot pressurized gas powers the rocket by expelling first water, then the gas itself out of the rocket nozzle at high velocity.
A few words of caution: water rockets pressurized with just air can be dangerous. Water rockets pressurized by internal combustion can be especially dangerous. The things described on this page look fun (and they are!), but they require a great deal of caution. Whenever I launch these rockets I exercise many safety precautions, the least of which is the wearing of eye protection and staying at least 8 meters away from the rocket while it is charged with fuel mixture.
The fuel source: water and electricity
For aesthetic reasons, I wanted to generate the combustion with water itself, so I fabricated a compact electrolysis unit that splits water into hydrogen and oxygen gases. This gas mixture is fed into the rocket and is ignited with a spark. After ignition, the two gases recombine and in the process release chemical energy that generates pressure.
My electrolysis unit, affectionately called “Mr. Splitter,” is actually four cells in series and is designed to be operated off a 12-volt source—I use a 12-volt 7-amp-hr portable lead acid battery. The unit draws about 10 amps of current, allowing it to generate about 0.5 liters/minute of fuel-gas mixture, composed of 2/3 hydrogen and 1/3 oxygen. The gas is carried to the rocket (mounted on the launcher) via quarter-inch vinyl irrigation tubing. Building the electrolysis unit took a great deal of painstaking work so that it operates safely and efficiently.
The launch platform
described here are the two launch platforms I constructed.
First-generation design
I constructed a simple launcher which is basically a half-inch PVC launch tube with a sparkgap at the top and a fuel-injecting conduit nearer the bottom. At the base of the launcher the PVC tube sticks through a hollowed-out 35mm film canister, the top of which forms a lip which the bottle sits on. Water drips out of the rocket as fuel gas is added. No O-rings, gaskets, cable ties, etc. are required because the rocket is never pressurized above atmospheric pressure.... until the moment after ignition.
The sparkgap is constructed of two copper wires (with insulation removed at the ends) which are connected to a remotely located piezo-electric sparking unit from a common fireplace butane lighter (the sparker can produce something like 18000 volts, but not enough current to harm a person). I found that the insulation on many wires I tried did not have sufficient dielectric strength to force the spark to jump only in the sparkgap. The top of the launch tube at the point of the sparkgap is sealed closed with hot glue. It is important that this area shed water well, as any water droplets stuck in the sparkgap will prevent the sparking. After charging the rocket with fuel for approximately 2 minutes, one click on the remote sparking unit is all it takes to send a rocket flying.
I learned (from sore experience) that the point where the fuel is introduced into the rocket must be below the water line. Otherwise, when the gas in the rocket is ignited, the combustion will travel through the conduit leading to the electrolysis cell. Shown below is the fuel-injector port located just above the film canister. Also pictured is a rocket mounted on the launch tube with bubbles of simulated fuel gas (actually air) entering the bottle through the injector port.
Based on a simple combustion model, I estimate that ignition of the pure fuel mixture (2/3 hydrogen, 1/3 oxygen) briefly generates a gauge pressure of 187 psig (12.9 bar). This means that the fuel mix inside the rocket should be diluted with at least an equal part of air to reduce the pressure so the rocket does not rupture upon ignition. I accomplish this by putting air and extra water in the rocket first and then watching as the fuel gas that enters the rocket displaces the water. By noting how far the water level has dropped I know how much fuel mix is in the rocket.
Second-generation design
My second-generation launch platform is built of metal in addition to PVC so that it is more sturdy and can launch a variety of rocket sizes.
The launch-tube portion is constructed of steel pipe. A movable stop and accompanying plate are machined out of aluminum. The base is constructed of PVC.
The pieces.
Bottom of the launch tube. The electrical wires and fuel hose
enter through a vertical slit.
Fuel-injection port with the stop placed just below it. The port
is located about halfway up the launch tube.
The top of the launch tube is sealed with polyurethane. Solder
was added to the protruding wires to decrease the size of the
spark gap. In this picture a spark is shown in the gap.
The stop can slide up or down the launch tube and is secured with
two screws.
The plate optionally sits on top of the stop and provides a
resting place for bottles larger than 2L. The circular grooves facilitate
centering of various bottle sizes.
Just about any size bottle will fit on the launcher: 1L, 2L, 3L,
19L, ...
Video of test launch
Here is a 19KB MPEG home video of a test flight made the night of Sept. 7, 2000 in the hills above Berkeley, California. The rocket is a naked 2-liter soda bottle. Just prior to ignition the rocket contained 600mL of fuel mixture and 140mL of water, with the remainder of the volume being air. Estimated gas pressure after ignition is 106 psig (7.3 bar) with an estimated temperature of 4467 oF (2464 oC). These results were predicted from a simple thermodynamic model.
The high gas temperature is the reason why the rocket glows briefly during launch (the rocket is like a neon light). The hot gas does not appear to harm the plastic rocket, probably because it doesn't stay inside for very long. The ignition and launch produce a distinctive “thunking” sound, but are no louder than an ordinary water-rocket launch. The bottle returns to the earth slightly warm to the touch and without the characteristic internal fog of conventional water rockets. Note that with an unaided eye the flash of light is not nearly so bright as in the video—I was filming at night with my Sony camera's “nightshot” mode on, which means it was picking up infra-red as well as visible light.